Always Employ a Venting
Ball Valve With Air Cylinder Operations
SHINJO material slide gates and diverters typically depend on compressed air like a source of energy to open and shut the blade of the slide
gate valve or diverter valve. Many air compressors are often able to supplying air pressure towards the air cylinder of 200 psi or greater, despite the fact that most dry SHINJO handling plants operate with compressed air within the 100-125 psi range. Slide gates and diverter valves utilized in dry SHINJO handling usually require less air pressure within the 80-100 psi range, but can handle handling pressure as much as 150 psi. The higher the air pressure towards the cylinders, the higher the speed and memory from the blade. Thus you are able to know how slide gates and diverter valves can deploy significant pressure when actuating and may cause serious injuries or dying otherwise used correctly and securely.
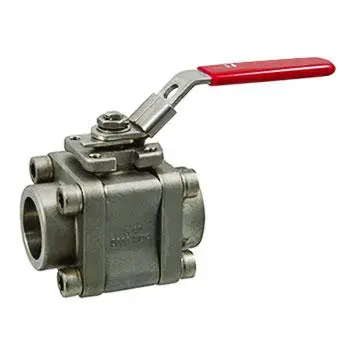
Warning-Sticker_Venting-Ball-Valve To avoid such catastrophes, it is best to make use of a venting ball valve, or residual pressure vent, with any air cylinder operated equipment. This can be done in four easy steps:
Remove electrical power in the air control set up,
Block or remove compressed air power within the compressed air lines,
Remove any residual compressed air power stored in mid-air cylinder, and
Perform safety tests to make certain all power sources happen to be removed.
The initial step of removing electrical power would be to correctly de-energize the gate. Slowly move the single cylinder slide gate towards the preferred position and find out the air cylinder’s two ports. The rear port drives the piston towards the front for that closing stroke from the blade to shut the gate. The leading port retracts the piston towards the back which opens the gate. For those who have a dual cylinder valve, the ports operate in the alternative direction, i.e., the rear port will open the gate, and also the front port closes the gate. Now you can turn off the ability towards the gate.
It's crucial to know that removing electrical energy towards the air control set up doesn't reduce a compressed air operated valve to some Zero Mechanical Condition (ZMS). Taking out the compressed air within the air cylinder of the slide gate or diverter valve is the best way to lessen the valve to some ZMS.
venting ball valve for pneumatic slide gates and diverter valves.The easiest method to take away the compressed air is to apply a venting ball valve, or residual pressure vent. A venting ball valve, correctly installed, prevents both compressed air from reaching the environment cylinder AND vents, or “bleeds off”, any residual downstream pressure within the air lines provided through the air cylinder. This enables any compressed air in mid-air cylinder or pressure within the lines to become exhausted, therefore lowering the gate or diverter to some ZMS to securely perform maintenance, obvious obstructions, or change material.
Where must i use a venting ball valve?
A venting ball valve ought to always be set up in the machine prior to the air cylinder from the air actuated valve to be able to bring the slide gate or diverter valve to zero mechanical condition (ZMS). The venting ball valves are usually set up in close closeness towards the gate or diverter’s air cylinder. It's suggested the venting ball valve be installed within easy arm’s achieve and clearly visible preferably between 12” (300mm) and 18” (450mm).
The number of venting ball valves must i have within my system?
Each gate must have one venting ball valve. It’s not essential, or suggested to possess a ball valve on every air cylinder like a valve having a dual cylinder actuation. Should you place a venting ball valve on every cylinder, then you would need to turn off each venting ball valve to show from the one valve. Many occasions this really is forgotten or even the worker is misinformed that venting one ball valve will turn the whole gate off.
Do you know the most typical accidents?Valve Receiving Hopper
The majority of the industrial accidents occur if you have a weighing
or calculating device downstream within the conveying line. Employees de-energize an element upstream in the gate, like a hopper, and wrongfully think that the whole product is shut lower. Then they attempt to obvious a blockage or change materials using their arm or hands within the road to a slide gate’s blade.
It should be clearly understood that de-energizing one component doesn't de-energize all components. If compressed air remains open to the gate throughout the cleaning process, as well as an action causes the size to achieve a collection point (e.g. leaning or sitting on the weigh hopper), the slide gate’s blade will close on anything in the path.
Many occasions, injuries takes place when a venting ball valve was connected to the system, although not used since the lock was permanently removed. Don't operate or service slide gates or diverter valves unless of course specific lock-out /tag-out procedures with this equipment have established yourself and enforced. U.S. federal rules require user from the equipment to determine an itemized insurance policy for training personnel and correctly performing lock-out/tag-out procedures to lessen the gate or diverter to some ZMS when installing, operating, or maintaining any powered gate or diverter. Lock-out/tag-out procedures aren't needed by European legislature, but inside the industry it's strongly encouraged to possess a written directive for safety.
Lock-StickerTo avoid this inside your plant, proper lock-out/tag-out procedures ought to be developed and adopted to make sure an additional safety precaution. A universal lock-out sticker emblem ought to be located close to the inlet and outlet of the valve. The venting ball valve also needs to incorporate a device for any lock to become put on its handle, stopping accidental return from the ball valve for an active position. Additionally, the finish user must train all people that use the equipment in the safe operation and be sure they've read and comprehend the written policy.